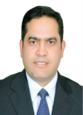
Abdelnasser Mabrouk
Hamad Bin Khalifa University, Qatar
Title: Novel design of multi effect evaporator for high performance of desalination plants
Biography
Biography: Abdelnasser Mabrouk
Abstract
This work presents a novel tube bundle arrangement of MED evaporator. The tube bundle is arranged to allow the generated vapor to flow in a smooth path and minimized route to reach the next effect. This route is designed in order to avoid shear loss to avoid breakdown of film liquid around tubes (dry zones) as a result not abruption the heat transfer process. Also this route will eliminate the vapor entrainment which reduce the brine carry over since there is no cross flow; consequently, there is no need for the demister. Also, the novel route is target to eliminate vapor boxes and directed the generated vapor in the current effect to the next effect through holes in the tube sheet. Also the holes of the tube sheets make sure the vapor is uniform distribution before the entrance to the next tubes bundle which eliminates the entrance loss. Process design calculations using VSP software showed that, for the same gain output ratio (GOR=9), the required heat transfer area of novel evaporator is 22% lower than that of existing evaporator. This is due thermal losses reduction (demister loss and vapor box loss) in the novel MED evaporator. The thermal loss reduction in the novel evaporator varies from 20% to 50%. Due to removal of demister in the novel MED evaporator, the evaporator width decreases by 65% however the novel evaporator height is almost double of the existing evaporator. The novel evaporator length is 6% lower than the existing evaporator. Due to reduction in the novel evaporator width and length, the foot print decreases by 65% lower than the existing evaporator. The cost of tubes of the novel evaporator is 18% lower than the traditional MED. This is mainly due to reduction in heat transfer area as a result of improvement of heat transfer process. Also, the shell material of the novel evaporator is 24% lower than that of the traditional MED-TVC. This is due to significant reduction in the evaporator width as a result of removing demister. The new design will minimize the thermal losses inside evaporator which will reduce the required heat transfer area and get a compact evaporator size. The expected reduction in heat transfer area not only reduces the capital cost of evaporator manufacturing but also will reduce the foot print of the MED desalination plant significantly.